Global Site
Displaying present location in the site.
Labor-saving and Unmanned Robotics Takes the Effort out of Physically Demanding Work
Cutting-edge Technologies to Build a Better Future: Advanced Technologies Permeate Every Facet of Our LivesWith its declining birthrate and aging population, Japan faces acute labor shortages ― especially in industries where physically demanding work is involved. In those fields where hard, physical labor is required, and where automation is more difficult to implement, the answer is robotics. In this paper, we look at two of the robotics systems NEC had developed in trial production projects run by Japan’s Acquisition, Technology and Logistics Agency (ATLA). One of these is a high-agility powered exoskeleton that multiplies the power of the operator and reduces the apparent weight load, while at the same time providing a high level of agility and usability on rough terrain. The other is a multi-purpose autonomous robotic vehicle that can operate on rough terrain without requiring priori map information. In addition to configuration and main component technologies, we will also discuss the projects in which these robots are being used and speculate on what possibilities the future may hold.
1. Introduction
As one of the world’s most rapidly aging societies, Japan now faces an unprecedented demographic crisis. Birthrates have been declining for years, leading to a steady decrease in the number of younger workers and an increase in the number of experienced workers who have or soon will retire. This problem is particularly vexatious in industries which involve physically demanding labor. The urgent need for workers has accelerated efforts to introduce robotics to reduce the demand for labor and facilitate unmanned operation of physically demanding work. Similar research into robotics is also underway in the defense sector where it is hoped that robots can minimize casualties as well as reduce labor requirements and facilitate unmanned operation.
In view of these challenges, NEC has developed a variety of robotic systems including, most recently, a high-agility powered exoskeleton and a multi-purpose autonomous robotic vehicle. These had been tested in trial production projects run by Japan’s Acquisition, Technology and Logistics Agency (ATLA), and are the subjects of this present paper.
2. High-agility Powered Exoskeleton
2.1 Background of the project
A powered exoskeleton is a wearable mobile machine equipped with functions that works in tandem with the user and provides the user’s limbs with increased strength and endurance. In consumer sectors, powered exoskeletons are currently used in healthcare to support patient rehabilitation and in logistics to lift heavy packages. In the defense sector, R&D into a powered exoskeleton is now actively being conducted in various countries, with the focus on use in a harsher environment and military operations. In Japan, research and development has also been advancing in the area of powered exoskeletons like the one introduced in this section, which is a prototype designed and produced in an ATLA trial production project called the High-agility Powered Exoskeleton Research Prototype1)2)3).
2.2 Configuration of the high-agility powered exoskeleton
In addition to reducing the burden of the equipment that weighs down soldiers engaged in missions such as amphibious operations and disaster relief, a high-agility powered exoskeleton can also enhance their speed, response time, and agility, as well as allowing them to move more easily over rugged terrain ranging from sand swept deserts to steep mountain trails. To achieve these requirements, the high-agility powered exoskeleton we have developed is configured so that it is worn on the legs with the mechanism that follows the motion of the wearer while the external skeleton structure bears the weight load. Photo 1 shows an external view of the high-agility powered exoskeleton.
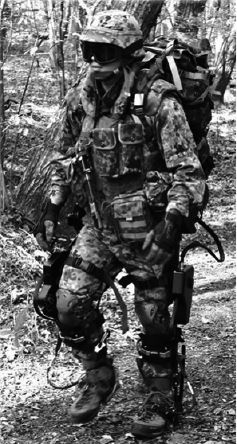
This powered exoskeleton is equipped with actuators in the hip joint and knee joints and with lightweight leaf springs in the ankle joints. By using the torque generated by the actuators to support the load and by transmitting the load to the ground through the exoskeleton’s frame, it alleviates the burden on the wearer. The main specifications of the prototype are shown in Table.
Table Main specifications of the high-agility powered exoskeleton.
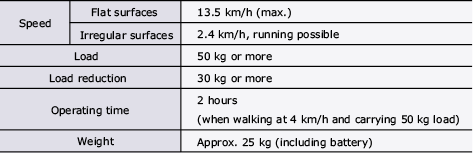
2.3 Main component technologies
The high-agility powered exoskeleton is built around three main component technologies.
2.3.1 High-response, high-output driving system technology
To facilitate agility and quick response while supporting a heavy load, the system driving the powered exoskeleton must be capable of high output and high response. We have optimized the actuators incorporated in the joints and their controls to allow faster motion such as running.
2.3.2 Irregular surface balance control technology
In military use, it is required that human balancing capability not be hampered even on an irregular ground surface. In addition to a frame that conforms to the user’s body, control technology is incorporated that responds promptly to any movement, accurately supporting the motions of the user on an irregular ground surface.
2.3.3 Safety assurance technology
As this is a machine that is actually worn on the human body, absolute operational safety is critical. To maximize safety, we conducted a risk assessment compliant with ISO 13482 Robots and robotic devices - Safety requirements for personal care robots4). By implementing safety measures based on analysis of risk sources, we have assured the safety of our powered exoskeleton.
2.4 Exoskeletons in the future
In order to put powered exoskeletons to practical use, NEC and the ATLA have subjected the current prototype to a battery of performance tests. In laboratory environment tests, the subject wearing the high-agility powered exoskeleton walked and ran on a treadmill while carrying load, while motion analysis was conducted using 3D motion analysis equipment. Tests on irregular ground surfaces were also conducted to evaluate maneuverability, wearability and other critical factors. Photo 2 shows outdoor functional verification of the prototype. As R&D into powered exoskeletons expands and various issues are solved, these machines will become ever more versatile and sophisticated, gradually permeating society and becoming a part of everyday life.
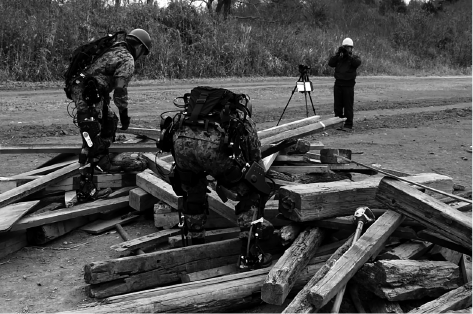
3. Multi-purpose Autonomous Robotic Vehicle
3.1 Background of the project
Autonomous driving technology for unmanned ground vehicles (UGVs) has been making rapid progress in the consumer sector in recent years. Validation tests of this technology are underway in various applications and industries such as autopilot for cars, automatic parcel delivery, and automatic heavy machinery operation. In some fields, this technology has already been put to practical use. In the defense sector, many countries are now actively conducting R&D and validation tests of UGVs focusing on operations pertinent to military use ― such as transportation of goods by truck convoy, disaster relief, and bomb disposal. The features of UGVs for military use include the ability to cope with extreme driving conditions such as unpaved roads and irregular surfaces, as well as the ability to operate reliably in an environment where detailed electronic map infrastructure is poor5).
Japan is also engaged in military-oriented R&D into autonomous driving UGVs. In this section, we introduce a prototype designed and produced in ATLA’s Multi-purpose Autonomous Robotic Vehicle Research Prototype Project.
3.2 Configuration of the multi-purpose autonomous robotic vehicle
The multi-purpose autonomous robotic vehicle consists of either one of two robots ― a wheeled vehicle robot or a tracked vehicle robot ― combined with an autonomous driving module that aggregates the software required to achieve autonomous driving as shown in Fig. 1.
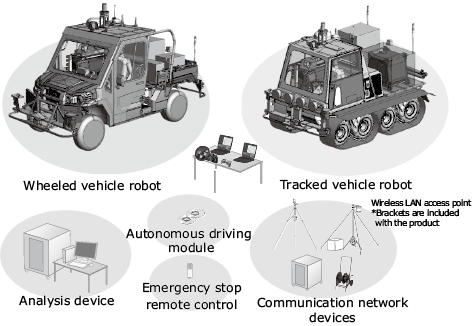
The wheeled vehicle robot is based on a dune buggy and developed for verification of autonomous driving performance mainly on paved and unpaved roads. The tracked vehicle robot is based on a tracked vehicle and developed for verification of autonomous driving performance mainly on unpaved roads and irregular surfaces. It also features a manipulator mounted on the rear of the vehicle for verification of remote-controlled manipulating work.
The main configuration of sensors installed on the wheeled vehicle robot is shown in Fig. 2. These sensors include 3D laser imaging detection and ranging (LIDAR) sensors, 2D LIDAR sensors, millimeter wave sensors, visible light camera, global navigation satellite system (GNSS) sensor, and inertial measurement unit (IMU) sensor. These sensors provide the data necessary for autonomous driving, enabling recognition of the environment around the vehicle, localization, path planning, and vehicle control.
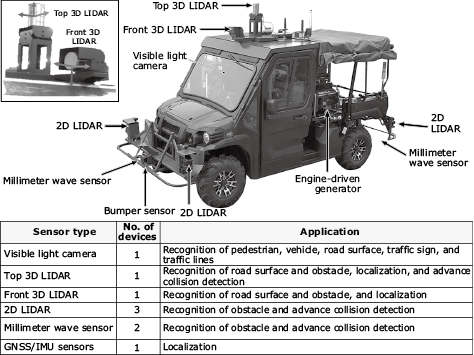
3.3 Main component technologies
Let’s take a look at the main component technologies used in the autonomous driving module to achieve autonomous driving on unpaved roads and irregular grounds.
3.3.1 Road surface recognition technology
Safe autonomous driving on unpaved roads and irregular surfaces requires the ability to recognize obstacles and uneven surfaces and optimize the vehicle’s travel to avoid or minimize the impact of these impediments by choosing a route better suited to the vehicle. To determine where the vehicle can be driven, the system processes the LIDAR sensor information and camera images as shown in Fig. 3. More specifically speaking, this technology combines geometric configuration information obtained by the LIDAR sensor and condition recognition results provided by the image recognition function, and then estimate the degree of drivability (whether the surface is suitable for driving). That estimate is then superimposed on the map information for the area around the vehicle. With the drivability estimate now combined with the map information, the vehicle can travel to the destination while generating a route suitable for driving and tracking that route. Additionally, we collect sensor data in environments where there are mainly unpaved roads and irregular surfaces, performing additional learning to improve the road surface recognition function.
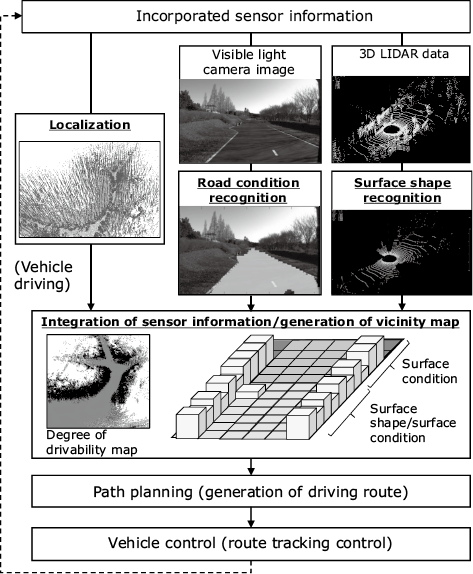
3.3.2 Self-position estimation
By combining the information from the GNSS sensor, inertial measurement device, and 3D LIDAR sensors, the vehicle robot estimates its position by itself. Because the characteristics of each sensor vary depending on the environment, we are also conducting trials to improve the localization performance to better suit each environment by integrating information according to the environment.
3.4 The future of autonomous driving
To improve the autonomous driving performance of our multi-purpose autonomous robotic vehicle, we have put it through a series of rigorous driving tests. We have also acquired powerful technological platforms from NEC’s research laboratories, including cutting-edge image recognition technology and learning technology that support autonomous driving performance on unpaved roads and irregular grounds. Going beyond mere autonomous driving, we are developing robot-user collaboration technology, swarm control technology, and so on, in order to help carry out missions and tasks more efficiently. Going forward, we will be applying these technological platforms to a variety of practical applications.
4. Conclusion
In this paper, we have shown the enormous potential of NEC’s robotics ― as demonstrated by our high-agility powered exoskeleton and multi-purpose autonomous robotic vehicle ― to achieve radical labor saving and facilitate unmanned operation of physically demanding work, as well as to optimize performance and reduce casualties in military operations. As Japan’s demographic crisis continues, robotics may come to the rescue in many fields, supporting and enhancing human labor in the defense sector as well as the consumer sector. Going forward, we will continue our efforts to promote NEC’s solutions for society through the pursuit of advanced ethical robotics.
Reference
- 1)
- 2)
- 3)Takuya Murakami, et al.: Powered Exoskeleton Technology, Defense Technology Journal August 2019, No. 461, pp. 4-11, August 2019 (Japanese)
- 4)ISO13482 Robots and robotic devices - Safety requirements for personal care robots
- 5)Shunei Harasaki, et al.: Research on Autonomous Driving on Unpaved Roads and Irregular Surfaces, Safety Engineering Symposium 2019 Preprints of Lectures, pp. 344-345, July 2019 (Japanese)
Authors’ Profiles
Expert
National Security Solutions Division
Expert
National Security Solutions Division