Global Site
Breadcrumb navigation
KITZ Corporation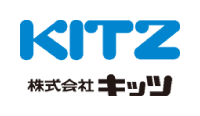
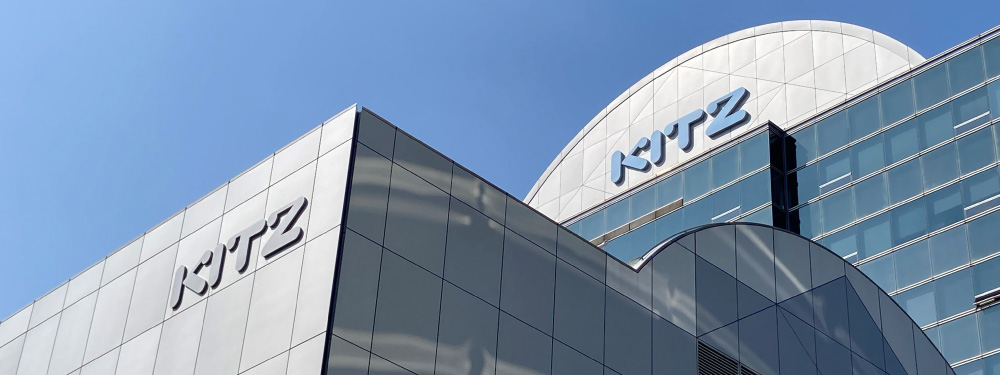

Automatic deployment of BOMs from engineering to manufacturing, starting from the 3D model
Further strengthening of unique strength of "100,000 ETO(Engineer To Order) per year" with PLM system
- Industry:
-
- Manufacturing
- Region:
-
- Asia Pacific
- Solutions:
-
- Others
- Integrated ICT Solutions
Summary
Challenges
- Business processes are extremely complicated due to Engineer To Order (ETO) that relies on paper and manual based work.
- There are limits to responding to globalization by host computer-based business application system which is operating 40-year.
- Eliminate the dispersion of information and make advanced use of it. Build an environment where KITZ can demonstrate own strengths.
Result
Advancement of Engineer To Order with information chain of engineering chain starting from 3D model
Built the system that automatically deploys 3D CAD, engineering BOM and manufacturing BOM from order specification, and link them to SAP system seamlessly. QCD (Quality, Cost and Delivery) has been significantly improved by streamlining the Engineer To Order while responding to wide range of product variations.
Inheriting own unique strengths to the order configurator in new system
The know-how implemented in full scratch system, such as coding of material combination patterns into and complicated specification variations, has been inherited in the new system. Current system could be reformed to the system that can demonstrate own uniqueness in Engineer To Order.
New platform for using 3D data-driven information has been set up
Various information is managed centrally from receipt of order to manufacturing. An environment has been built to create added value such as developing next generation standard products and providing new maintenance services by analyzing and utilizing the collected and accumulated information.
Implement Solution
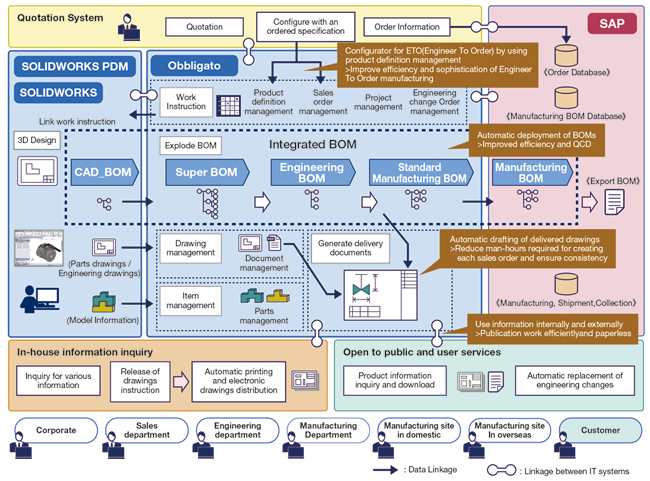

In PLM, production results and specification suitability are judged on the basis of order specification information linked from quotation system and Engineer To Order products are designed in 3D with SOLIDWORKS. Starting from 3D model, system that explode CAD BOM, Engineering BOM, Manufacturing BOM automatically and links these BOMs to SAP system seamlessly, is implemented
Detail
Challenges
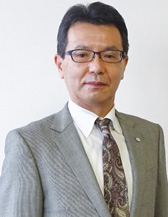
Executive Officer
General manager, Valve manufacturing business
KITZ Corporation
Difficult to maintain a complex system over 40 years of operation
Valves that control the flow and stops of fluids such as water, air, oil, and gas, which are indispensable for our daily life and industry. It's KITZ, a comprehensive valve manufacturer that responds to these diverse needs through material development and integrated production. The company's valve products, which are developing business globally, support the society by controlling fluids in a variety of places, including petroleum and chemical plants, process lines for machinery, LNG (Liquefied Natural Gas) terminals, and building air conditioning systems.
Mr. Yukinari Koide of KITZ says that "The requirements and specifications for valves vary significantly depending on the type of fluid flowing through the pipes. Depending on the type of fluids, unique shapes have to be designed by using special materials and corrosion-resistant process. Our strength lies in our ability to respond to the detailed needs of our customers not only for standard parts but also custom designed products that are Engineer To Order by handling the entire process from material development, casting to engineering and manufacturing".
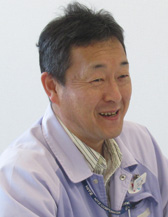
Engineering division
Custom engineering department head
KITZ Corporation
In order to deal with Engineer To Order products, KITZ has established a unique logic-based order, engineering, manufacturing, financial and accounting process. In the past, these processes were reflected in the host computer-based system with scratch development, but the system had become more complicated over the 40 years of operation and modification. Therefore, it has become difficult to maintain.
In addition, "evolving into a truly global company" is an important pillar of the management plan, and to achieve this, it is necessary to support globalization such as changing the system to multilingual and operation hours, as well as to link with peripheral systems and solve issues for digital transformation (DX). It was against this background that we need to renew the platform.
Hiroshi Ando of the KITZ Corporation says that "Most of the linkage between peripheral systems and the core system, such as the registration of BOMs after receiving engineering data created by CAD, was dependent on paper and manual based work. Due to the characteristics of valves, there are a wide variety of variations in specifications such as different materials and special coatings depending on the operating environment and fluid conditions, and with the strength of handling custom specifications, the workload is enormous as the number of Engineer To Order reaches 100,000 numbers per year. Furthermore, the deliverables of each process, such as engineering drawings and calculation sheets, are scattered in various places, therefore it is difficult to search and reuse them. In order to improve these processes, we needed a new system."
Solution
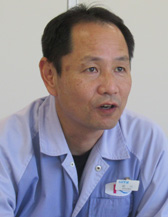
Engineering division
New Engineering Center
Engineering System Group, Group head
KITZ Corporation
Propose an ideal system by using our experiences:
Therefore, KITZ decided to renew their IT system in order to strengthen their management system as part of their mid-range plan. The main pillars of the project were to adopt a package-based system instead of a full-scratch system, to migrate to 3D design for more sophisticated design, to build a PLM system that centrally manages the information related to the engineering chain of make to order, engineering and manufacturing and to link this engineering information with ERP system.
As a specific solution, initially KITZ decided to implement SOLIDWORKS for 3D CAD and SAP ERP for ERP system. In addition, they adopted NEC's Obbligato for PLM system.
Takashi Aikawa of the KITZ Corporation says that "First, we evaluated Obbligato's implementation record. NEC has an overwhelming track record for implementation of Obbligato especially in Japan. In addition, NEC's experience and knowledge supported our company for adopting PLM. NEC understands the process we want to implement, and also incorporates its own knowledge into the system. We decided to hire NEC as our partner because we highly appreciated their proposal to design the system from a long-term perspective in anticipation of future modifications that may occur. In addition, Obbligato has a standard function for managing specifications, functions, and variations to handle a wide variety of make to order, which is one of our company strengths. Having such features in a standard function was the strength of the NEC that no other company had.
Result

Engineering division
New Engineering Center
Standard BOM Group, Group Head
KITZ Corporation
Automatic deployment of BOMs from CAD to SAP system through PLM based on order specifications
The new system is literally the "core" system that will support KITZ in the future. Our company worked with NEC on the project step wise and carefully to ensure that the IT system migration would not have any impact on operational efficiency.
The completed IT system seamlessly links SOLIDWORKS to SOLIDWORKS PDM, Obbligato and SAP system. It has automated the generation of various BOMs, including not only for standard products but also for Engineer To Order product, where mistakes and inconsistencies had been occurred due to manual work and re-input, and has also contributed to the significant improvements in QCD by linking the information seamlessly starting from 3D model to receipt of order, engineering and manufacturing.
Atsushi Okubo of the KITZ corporation explains that "Order information is linked from quotation system to SAP system and order specifications information is linked to Obbligato. Obbligato has built-in "product definition management" that manages variations in product specification options and also make judgments on the suitability of combination of order specifications such as product range conditions and ancillary configurations and then order information is applied to determine if order can be processed. If such order can be processed, then BOM will be automatically exploded by referring to past design result"
Patterns such as combination pattern of coded materials is a unique know-how that our company has accumulated. This strength has been inherited from existing to the new system. If there was no appropriate track record in the past, the product is determined to be custom design products and the engineer will be asked to design it, but of course, the deliverable will be later registered as a track record and it will become make to order products whose BOM will be automatically exploded from next time.
Mr. Aikawa says that "In order to handle complex and diverse variations, we have implemented a system that seamlessly links five BOMs: a CAD BOM linked from 3D CAD as a starting point, a Super BOM that consists part numbers of all selectable parts, engineering BOM that explodes the part configuration for each product item, standard manufacturing BOM that adds process part numbers which are required for arrangements, and manufacturing BOM that adds arrangement attributes in SAP system. Currently, about 80% of orders are automatically exploded with BOM, which has led to a significant increase in efficiency. In addition, by linking CAD, PDM and PLM, the delivery documents that were created for each order such as drawings, BOM, specifications are now created and configured automatically and also inconsistencies in the documents used to exchange make to order specifications with customers are eliminated. These are the key points that have improved the efficiency".
In addition, all technical information is linked and collected in the form order information in Obbligato. It is also a great achievement that it has become possible to smoothly search for past assets and use them for secondary purposes.
Mr. Koide emphasizes that "For example, we analyze customer needs from order information and support engineers to utilize it for the development and design of the next standard product. Furthermore, taking advantage of the fact that all information from order to delivery can be traced immediately. We feel that there are various possibilities, such as providing the new maintenance services."
Modernize the system while inheriting the know-how that has been accumulated for many years. Based on that system, we will promote the development of products and services that make advanced use of data. The company's efforts are truly known as "MONOZUKURI DX". It is a great effort to accelerate the company's growth.
Comment of NEC's members
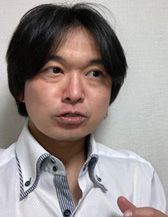
Product engineering division
Assistant Manager
NEC Solution Innovator
Contribution to the optimization of entire engineering chain
The important point in KITZ Corporation project was to deal with huge number of product variations. "Product definition management" application of Obbligato has made the significant contribution in solving this issue. This function shows the combination of product specifications, functions and ancillary configurations such as "Valve diameter, "Material type", "Actuator type" on the matrix. By referring to this information as master information, new system makes the judgment whether to accept or refuse the order and use it as a basis for automatic deployment of BOM.
As represented by this function, various add-on function can be added to the Obbligato. In this case, we were able to contribute to the sophistication of custom order design, which is one of the KITZ's strength, due to its flexibility.
In addition, we believe that key factor in the success of the project was that NEC was not able to manage only the implementation of Obbligato but also the implementation of SOLIDWORKS which is 3D CAD tool.
This is because, NEC has extensive experience and Know-How in SOLIDWORKS and also NEC has able to execute its strength to optimize and transform the entire manufacturing process from engineering to manufacturing. The Obbligato and SOLIDWORKS team will continue to work closely and contribute to the total optimization of KITZ's engineering chain.
Customer's Profile
KITZ Corporation
Address | 1-10-1 Nakase, Mihama-ku, Chiba-shi, Chiba pref. 261-8577, Japan |
---|---|
Established | January 26, 1951 |
Number of Employees | 5,090(Consolidated)、1,383(Non-consolidated) |
Overview | A manufacturer of valve products that control fluids such as water, oil, steam and gas. Based on the philosophy of "always making better products cheaper and faster", KITZ has established a formation and system that enables it to hand all process from casting of raw material to processing, assembly, inspection, and shipment on their own based on integrated production. |
URL | ![]() |
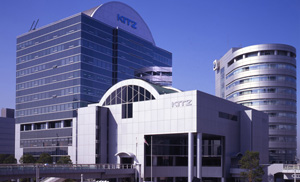
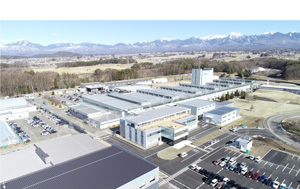
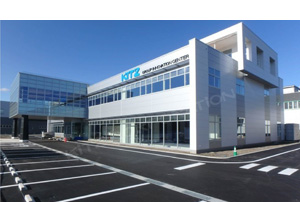

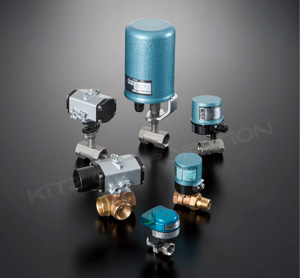
Related links
More case studies
(MAR 25, 2022)