Global Site
Breadcrumb navigation
Bioplastics for Electronic Equipment
Featured TechnologiesAugust 2016
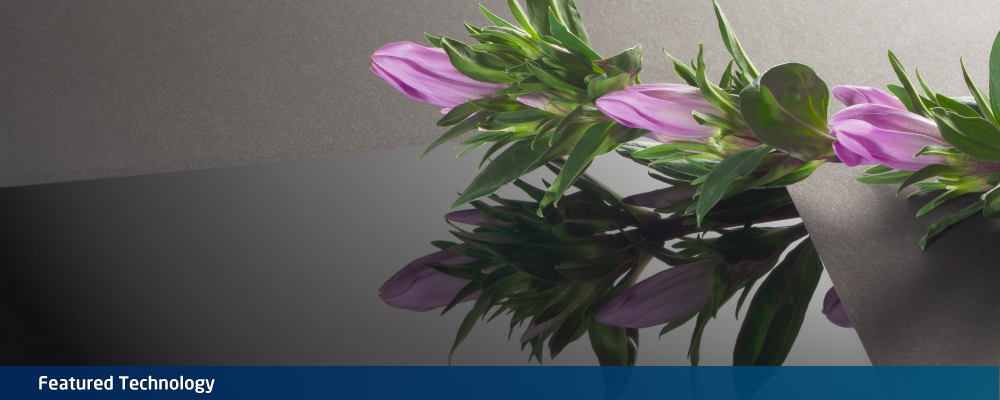
- 1. The beginnings of environment-friendly plastics development
-Environment-friendly petroleum-based flame-retardant plastics- - 2. From petroleum-based plastics to baiomass-based plastics (bioplastics)
- 3. Tackling the development of biomass-based plastics
-(Bioplastics) for electronic equipment- - 4. Commercialization and further development
Many enterprises and organizations would like to expand NEC engages in a broad variety of environmental initiatives, and conducts R&D to develop technologies to reduce environmental impacts. One of its research projects deals with the recently topical subject of environment-friendly bioplastics, made from plant-based raw materials.
In 2006, we adapted and commercialized a cell phone (FOMA-N701iECO) that uses a kenaf fiber-reinforced bioplastic for its external covering. In January 2010, we commercialized a business personal computer that in 90% of its plastic housing uses, which is one of the most environmental-friendly flame-retardant bioplastic in the world.

Here, research fellow, Dr. Masatoshi Iji offers an introduction to high-safety petroleum-based flame-retardant plastics, which were the first kind environment-friendly plastics NEC worked on in the course of its development work. He then proceeds with a detailed presentation on the effort NEC has been making in recent years to develop bioplastics that are even more environment-friendly.
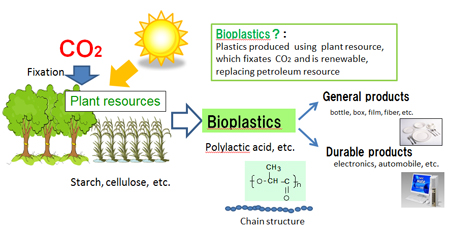
1. The beginnings of Environment-friendly plastics development
-Environment-friendly petroleum-based flame-retardant plastics-
We began working on the development of environmentally friendly plastics about 10 years ago. At that time there was virtually no concept of using such materials for electronic products, so we started out as pioneers. We set out by trying to improve the environmental safety of petroleum-based flame-retardant plastics. For reasons of fire safety, plastics used for electronic equipment must be resistant to fire, i.e., flame-retardant. To make conventional plastics flame-resistant, substances with flame-retardant properties, such as halogen compounds were used as additives. However, when these halogen-type flame-retarding addditives are burned they generate substances that are highly damaging to the environment. Furthermore, the phosphorus compounds used as substitutes for the halogen-type flame-retarding addditives are feared to cause chronic toxicity. So the environmental safety of such additives was a serious concern.
Focusing on the problem, we took up the challenge of making flame-retardant plastics with greatly improved environmental safety, by developing advanced flame-retarding additives free of halogens and phosphorus.
Thus we developed a flame-retardant polycarbonate resin (EKOPORIKA:Japanese Trade Mark) that features an original silicone-type flame-retarding additive that forms a flame-resistant layer on the resin surface at the time of ignition, and we successfully used these for the first time ever in electronic equipment. (See Fig.1.) EKOPORIKA has been jointly commercialized with Sumitomo Dow Ltd., and currently it is used as the main casing material for NEC's eco-friendly product lines of personal computers. It is also now finding application in various other fields. In addition, we also developed a self-extinguishing epoxy resin compound that does not require any flame-retarding additive because the resin itself blisters and forms a thermally insulating foam layer when exposed to flames. (Self-extinguishing epoxy resin compound) This self-extinguishing epoxy resin compound was commercialized in partnership with Sumitomo Bakelite Company Co.Ltd., as a molding material for IC packages, and in addition to NEC it has been adopted by many of the world's leading device makers.
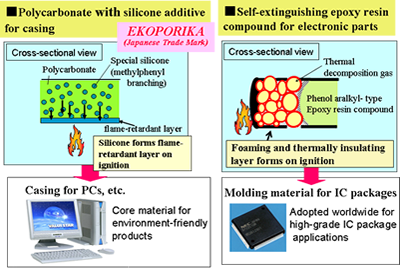
2. From petroleum-based plastics to baiomass-based plastics (bioplastics)
As described above, the casing of electronic equipment and insulating materials of electronic parts are conventionally made of petroleum-based plastics (polycarbonate, ABS, epoxy resin, etc.), and work continues on trying to make these materials more environmentally safe. However, with the current rapid depletion of petroleum resources, the search for alternative, renewable resources has become a new focus of concern.
One kind of material that is being developed is bioplastic, made of plant-derived materials (biomass). As an alternative to petroleum-based materials, biomass-based materials have distinct advantages, such as the ability to fix the CO₂ gas that causes global warming, and superior degradability (biodegradability) in the soil after disposal. Bioplastics are currently being looked at as a highly promising environment-friendly material.
3. Tackling the development of biomass-based plastics
-(Bioplastics) for electronic equipment-
Bioplastics can be classified into three basic types, according to how they are made: by microbial production, by chemical synthesis, and by natural processes. Polylactic acid, for example, is being mass-produced by chemical synthesis using raw materials derived from corn. Due to the fact that it has a relatively high heat-resistance for a bioplastic, it is already being used for some parts of the casing of electronic equipment.
However, before it can be used more widely in electronic equipment, the material performance of polylactic acid needs to be enhanced further. It is still significantly inferior to conventional petroleum-based plastics for heat resistance and strength (e.g. impact strength), and it has not yet been possible to make a high-safety, flame-retardant formula (without halogen additives). In addition, resin crystallization rate is slow during molding, so its moldability needs to be improved too. A number of companies are pursuing technical development work to overcome these problems, but up to now, most of their formulas contain a large quantity (approx. 50%) of petroleum-based components, such as petroleum-based plastics, which reduces the environmental benefits offered by polylactic acid bioplastics.
Thus at NEC we are striving to improve the performance of polylactic acid so that it can be used in electronic equipment, so as to fully preserve its environment-friendly properties (high biomass-based component ratio + safety). This is done by using predominantly biomass-based additives to improve its practicability, and also through research on how to enhance it with added value by endowing it with desirable new properties. More specifically, we are making polylactic acid formulas that display excellent heat resistance and mechanical strength, using biomass-based additives such as kenaf fiber, which offers a high global-warming prevention factor. On top of this, we have successfully achieved flame retardancy without using any harmful substances such as halogens, by incorporating environmentally safe, heat-absorbing additives (metal hydroxides). Currently, we are working to develop bioplastics that offer a performance attribute that has not yet been achieved: the combination of shape memory and recyclability.
Kenaf fiber-reinforced polylactic acid
To enable polylactic acid to be used for the casing of electronic equipment it is necessary to greatly improve its heat resistance, strength, and formability. We therefore worked to improve these characteristics by combining biomass-based additives such as kenaf fiber. As a result we developed a new composite material: kenaf fiber-reinforced polylactic acid. (See Fig. 2.) This material boasts the highest biomass-based content (90% of resin content, excluding inorganics) of any bioplastic for electronic equipment.
Kenaf is a plant originally grown in Africa, with one of the highest rates of CO₂ absorption of any plant. (Its photosynthesis rate is 3 to 9 times higher than ordinary plants resins, and it is capable of absorbing approx. 1.4 tons of CO₂ per ton of kenaf.) It is thus a very effective plant in terms of global warming prevention. It is now being cultivated in Southeast Asia and many other countries around the world, mainly as a substitute for existing materials for uses such as paper fiber and livestock feed. No high added-value uses of the plant had been developed before now.
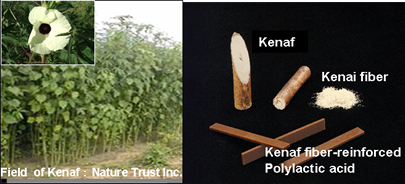
The results of tests conducted by adding and kneading in kenaf fiber with polylactic acid to enhance stiffness show that the addition of 15% or more of the fiber results in better heat-resistance (deflection temperature under load) and modulus than that of petroleum-based ABS resins. (See Fig. 3.) This effect was found to result not only from the fact that kenaf fiber inhibits the deformation of resin, but also by its ability to promote crystallization of polylactic acid. We also found that the removal of kenaf particles and the addition of plant-derived agents to promote ductility resulted in improved impact strength. Furthermore, by combing kenaf fiber with a new crystallization promoter, it is possible to cut molding time from more than five minutes down to less than one minute. We were thus successful in dramatically improving moldability.
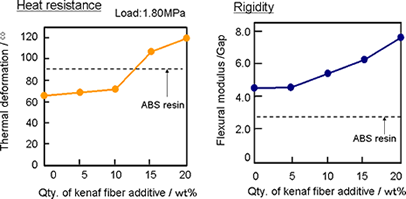
This kenaf fiber-reinforced polylactic acid was commercialized jointly with Unitika Ltd. in September 2004, when the material was used to make the dummy card for a personal computer. Then in March 2006 the material was adopted for the casing of an "eco" mobile phone. (See Fig. 4, and March 20, 2006 press release.) This was the first mobile phone in the world with a casing made mostly of bioplastic. The phone was designed to take advantage of the unique quality of this bioplastic material, i.e., color tones to evoke a gentle, soothing feeling, and the lack of a thick coating, to allow the special touch of the material to be felt. The product made a significant impact!
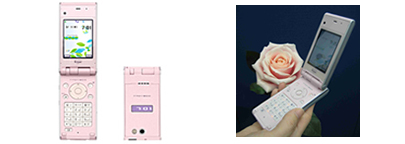
Flame-retardant polylactic acid composite
Plastics used for the external casing of medium-sized and larger electronic equipment such as personal computers require a high degree of flame retardancy. Since polylactic acid (PLA) is quite easily flammable, its flame retardancy needs to be improved before it can be used for such applications. As described above, conventional flame retardants such as halogen are environmentally unsafe, so we attempted to produce a flame retardant PLA composite without using these substances.
In November 2009, we developed the first practical application of the PLA composite. It is one of the most environmentally friendly flame retardant bioplastics in the world because it is composed of more than 75 percent plant-based material and emits only half the carbon dioxide during its life cycle, compared to existing petroleum-based plastics (such as PC/ABS).
We have adopted it as part of our goal to produce environmentally responsible products, and we are using it in business computers that we sell commercially.
The PLA composite has been used in business terminals, projector, and point of sale system (POS)
Furthermore, to expand its use in various electronic equipment and other durable products, we have improved the durability including the resistances to chemical agents (alkali cleaner, oil, etc), scratch and light, and anti-bacteria, which are higher than those of conventional petroleum-based flame retardant plastics (PC/ABS resin) used in electronic products. Thus, we aims to expand use of the PLA composites for facilities and equipment supporting the infrastructure in a wide range of industries, including distribution, transportation, and finance. First of all, we have begun applying the bioplastic for internal components of outdoor gas station fueling systems, which require reliable chemical resistance for gasoline and high dimensional stability in particular.
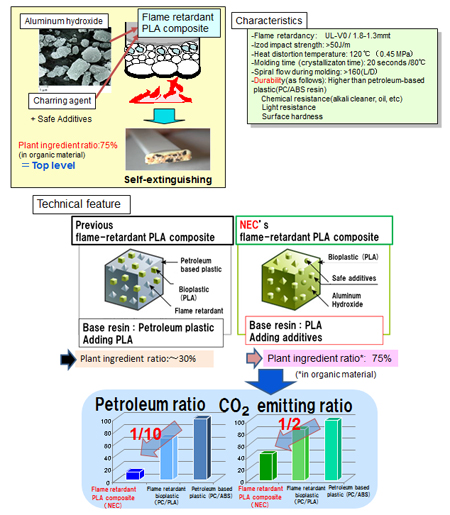

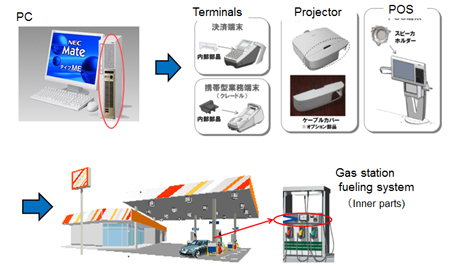

Bioplastics combining shape memory and recyclability
Since polylactic acid is still an expensive material, its widespread adoption will remain limited, despite its superior environmental performance. One way to try and overcome this limitation is to try to enhance its value as a material, by endowing it with new properties not available in conventional materials. With this objective, we succeeded in developing a polylactic acid that combines shape memory and recyclability, two characteristics that cannot be achieved with conventional petroleum-based plastics.
Shape memory plastics are plastics with the following ability: If they are deformed using heat and external force, then cooled and hardened, when they are heated again they return to their original shape. Generally, this characteristic is seen in plastics having a cross-linked structure (mesh structure). Unfortunately though, due to their cross-linked structure, such plastics do not melt, even at high temperatures, so recycling them (reforming them into different shapes) is difficult.
Needing to solve this problem, we developed a technology to achieve thermo-reversible cross-linking in the structure of the polylactic acid, resulting in materials displaying a combination of shape memory and recyclability. Thanks to this cross-linked structure, the material can be deformed and restored to its original shape by heating at the temperature of a hairdryer (approx. 60°C), but if heated to a typical molding temperature (160°C) the cross-linked structure dissociates, causing the material to melt, thereby enabling easy recyclability. (See Fig. 6.)
This recyclable, shape memory bioplastic allows users to freely deform the material into any shape they like, making possible all kinds of new products and applications, like futuristic wearable electronic equipment for example. (See Fig. 7.)
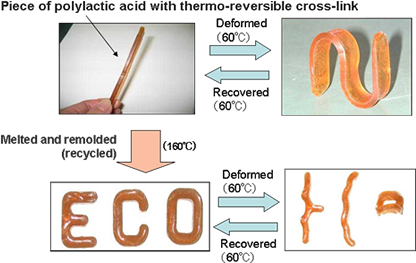
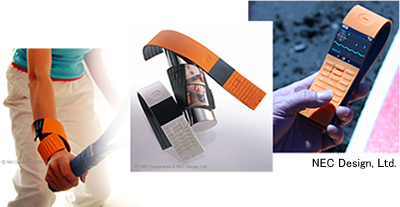
High-thermal conductivity polylactic acid composite materials
Following the addition of shape memory, as described above, we further increased the added value of polylactic acid by developing a polylactic acid composite of high thermal conductivity that can contribute to better heat dissipationa major issue in the design of today's electronic equipment. As electronic devices become ever smaller and thinner, the rise in temperature inside their housing, due to internal heat generation, is becoming a serious challenge, but it is difficult to deal with this using conventional parts for promoting heat dissipation, such as fans and sheets. In addition, when stainless steel or other metallic material is used for a device housing, heat conductivity is high only in the direction of the thickness, resulting in localized points of high temperature around the outside of the device, and to discomfort during use. Furthermore, since metals have a higher specific gravity than plastic, it is more difficult to reduce their weight and more demanding to form them into complicated shapes.
A conventional method of increasing the thermal conductivity of plastic is to include, in a petroleum-based plastic, a high proportion (≥ 50%) of a high-conductivity material such as powdered metal or carbon, or fiber. In practice, however, this method presents problems such as reduced formability and strength, and an increase in specific gravity. Also, since this plastic is made from petroleum-based raw materials, it is not very environment-friendly.
In addressing this problem, we succeeded in producing polylactic acid of higher thermal conductivity using a significantly lower amount of added carbon fiber (≥ 10%), using polylactic acid (a type of bioplastic) as a base resin, and an original plant-based binding agent to achieve reticulate (mesh-shaped) bonding (cross-linking) of carbon fibers in resin. (See Fig. 8.) This material has a low specific specific gravity (≤ 1.3)close to that of polylactic acidand combines a thermal diffusivity that is better than that of stainless steel, while keeping the typical light weight of plastics. (See Fig. 9.) Furthermore, we achieved anisotropic heat transfer in the planar directiona feature that cannot be achieved with metalsby means of orienting the carbon fibers during the formation process. (See Fig. 10.) When this material is used for the housing of today's increasingly small and thin electronic equipments, these features will enable good heat dissipation from the housing without allowing localized points of high temperature. They will also prove useful in various other fields of application.
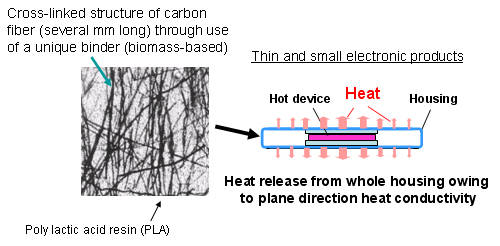
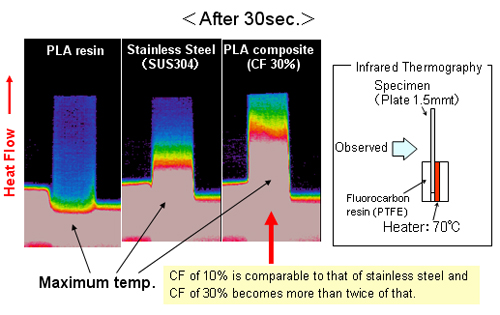
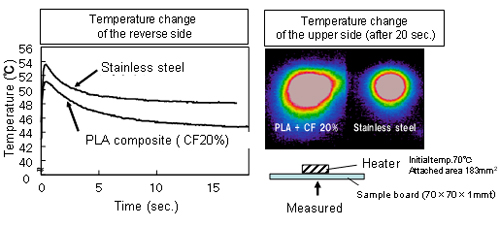
Three-layered nano-filler for toughening bioplastic
Regarding baioplastics including polylactic acid as a base resin , further improvement in the material's toughness is required to respond to needs for smaller and thinner devices in the future. As a technology to solve this problem, we have developed a nano-sized filler, or nano-filler, with a triple-layer structure. By adding this filler to polylact nano-sized particle filler (nano filler) dramatically improving the resin's toughness.
This technology is a fundamental technology that can be adapted equally to all our high-performance bioplastic materials (polylactic acid with added kenaf fiber, flame retardant polylactic acid, shape memory polylactic acid, heat conductive polylactic acid), which I introduced previously.
The main feature of this three-layered nano-filler that we have developed is that it can form, in a self-organized fashion, nano-size particles that have different functions in the three layers. It can be formed by agglomeration and condensation of unique organic silicon compounds that have three units. Until now, a multi-stage operation of separation and recovery of the surface finishing and processing chemicals was necessary to form multi-layered filler. This operation was difficult and time-consuming, and, particularly in the case of nano-sized particles, production, was substantially difficult. Yet now with this research it has become possible for the first time to form a three-layered structure efficiently.
The structure of this nano-filler consists mainly of high-density (high rigidity) siloaxane, with an inner layer of flexible silicone rubber and an outside organic layer of caprolactam, which has a high affinity with polylactic acid. For this reason, when mixed with polylactic acid, the filler has the rigidity of conventional inorganic fillers, yet shows improvement in absorbability from its rubber layer and improvement in plasticity from its organic affinitive layer. As a result, by adding a small amount of this filler to polylactic acid (5% by weight), we were able to improve the breaking elongation by more than two times, while still maintaining the polylactic acid's strength.
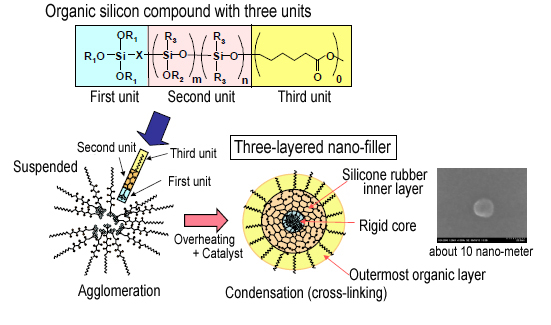
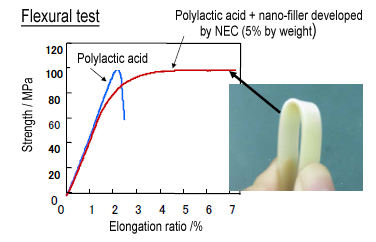
This technology is effective for toughening bioplastic used on exterior covering, and we believe it will help to make electronic device housing using bioplastics thinner and more durable. In particular, we aim to move forward with achieving cost reductions and optimization of the structure of this nano-filler and develop its commercial viability.
- *Cross-linking: connecting chain and branched polymers and converting them into an interlocking structure, like that of a net
High Performance Bioplastic with a High Plant Ratio by Using Non-edible Plant Resources: Plant Stems and Cashew Nut Shells (Cellulose Resin Bonded with Cardanol)
We have developed a first-of-its-kind durable new bioplastic that is produced from stable, non-edible plant resources. The bioplastic is created by bonding cellulose, a main component of plant stems, with cardanol, a primary component of cashew nut shells, which achieves a level of durability that is suitable for electronic equipment and boasts a high plant composition ratio of more than 70%.
Polylactic acid (PLA), a representative of mass-produced bioplastics, which NEC uses in the PLA composites above mentioned , primarily uses starch made from feed grains (old crops) as a plant resource, and therefore, its usage does not cause to conflict food at present. However, the future possibility of food shortages has drawn attention to the importance of using non-edible plant resources to produce bioplastics.
Therefore, bioplastics produced from non-edible plant-based materials have been developed using such resources as cellulose and castor oil. Cellulose, the world's most abundant non-edible plant resource is a main component of grass stems, crops and wood; the annual available amount is comparable to that of petroleum. Cellulose-based bioplastics have conventionally been utilized in such products as stationery, toys and household goods. However, these cellulose bioplastics require large amounts of petroleum-based additives such as plasticizers, which results in bioplastics with a low plant component ratio and poor durability, including insufficient heat resistance and water resistance. A polyamide resin derived from castor oil, a non-edible plant resource is also being used, however, there is an inadequate supply of this plant resource to expand its use and its characteristics are unsuitable for use in a variety of durable products, including electronics.
To resolve these issues, we have developed a new bioplastic by using cellulose as the main ingredient and cardanol as a modifier to react with cellulose (cardanol-bonded cellulose resin). Cardanol is an oil-like material extracted from cashew nut shells, which are often a discarded byproduct of the agricultural process, and represent a non-edible plant-based resource with a stable supply. Cardanol has a unique molecular structure consisting of a flexible and hydrophobic component: liner hydrocarbon and a rigid component: phenol. Therefore, after enhancing its reactivity, chemically bonding the modified cardanol and acetic acid with cellulose produces a durable bioplastic that is strong, heat resistant, water resistant and non-crystalline (short molding time compared to petroleum based plastics). The use of cellulose and cardanol, both plant resources, as the plastic's primary components produces a plastic that features a high plant component ratio of more than 70%.
We has developed a new production technology which allows it to produce the cardanol-bonded cellulose resin using just one-tenth the energy (fewer CO₂ emissions) that was previously required for processes using the non-edible plant resource of cellulose and natural oil as raw materials. --> May.8.2014 Press Release
In the new two-stage heterogeneous synthesis process developed, instead of dissolving the raw material cellulose into an organic solvent (homogenous system) as before, after being swollen into a gel-like substance with an organic solvent (heterogeneous system), it is bonded with the modified cardanol and acetic acid in two stages to synthesize a resin. This resin can be easily collected from a liquid solution through solid-liquid separation methods such as precipitation and filtration. As this process achieves the reaction conditions at almost ordinary pressure and medium temperature (100°C or less), and does not require a solvent for separation of the produced resin, as was required with the conventional homogeneous process, a significant reduction in the amount of solvent needed for synthesis (a roughly 90% decrease from the conventional process) is achieved. As a result, this cellulose-based high-functionality bioplastic can be produced for about one tenth of the energy (CO₂ emissions) when compared with conventional methods, thereby promising a drastic reduction in production costs when the material is mass produced in the future.
Moving forward, NEC plans to complete techniques for mass production while expanding the current scale of production (laboratory level) based on the newly-developed production technique in stages, with the aim to commence mass production during fiscal 2016.
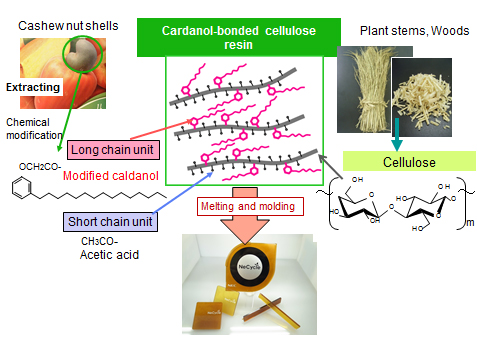
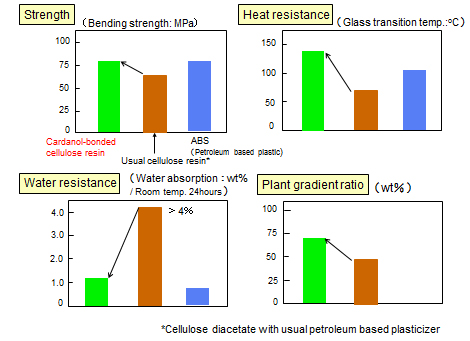
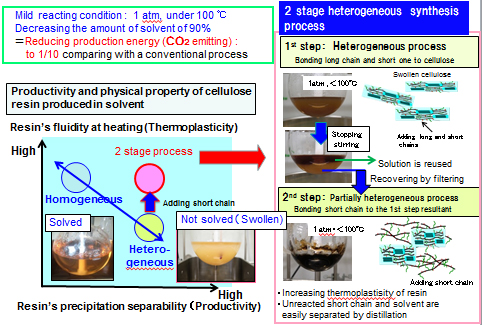
Development of 2-stage heterogeneous synthesis process
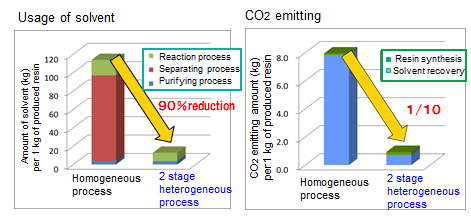
Development of non-edible-plant-based bioplastic featuring the elegance of traditional Japanese lacquerware (Urushi black tone bioplastic)
NEC has developed non-edible-plant-based cellulose-type bioplastic (*1) realizing elegant black color (Urushi black) of traditional Japanese lacquerware, which is highly regarded internationally (*2). (Collaboration with the Kyoto Institute of Technology and a representative Japanese lacquerware artist, Dr. Yutaro Shimode (*3))
Aiming at applying bioplastic to various durable products, NEC has tried to realize a new additional value, "decorativeness" (excellence in design), in addition to former functions such as durability.
In order to create the new cellulose-based bioplastic, NEC developed a unique technology for mixing additives to adjust coloration and light reflectance of the material, enabling, for the first time, the realization of optical properties (low brightness, high glossiness, etc.) similar to the deep and shiny "Urushi black" color of high-grade Japanese lacquerware. Since manufacturing of lacquerware involves repeated manual processes, coating with lacquer and polishing of the product, its mass production is difficult. The new bioplastic, in contrast, can be mass-produced into products of various shapes by ordinary injection molding process (*4) for plastics.
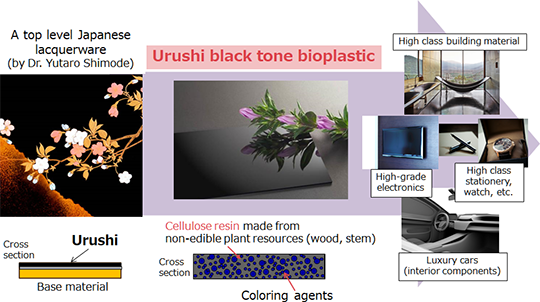

Efforts are underway to mass produce bioplastics deriving from sustainable plant resources to help resolve the issues of global resource depletion and climate change. Furthermore, owning to concerns about a future food shortage, new bioplastics from non-edible plant resources are increasingly required. Cellulose resin, which is made using the main ingredient of non-edible plant resources such as stems of cereal crops and wood, has already been used in stationery, toys, and everyday items. To expand the scope of applications for use, creation of features offering new added-value is demanded as well as environmental friendliness. Therefore, NEC aimed at achievement of high decorativeness, in addition to environmental friendliness and functions such as durability (heat resistance, water resistance, etc.). It became clear that the "Urushi black" coloring of high-grade Japanese lacquerware is highly regarded especially in Europe and the United States through detailed market research, and therefore the realization of "Urushi black" was targeted.
A cellulose-based bioplastic realizing the "Urushi black" has been developed in collaboration with a representative Japanese lacquerware artist, Dr. Yutaro Shimode (the third-generation president of the Shimode Makie Studio and a professor at the Kyoto Sangyo University) and the Kyoto Institute of Technology's Future Applied Conventional Technology Center, which is famous for future applied conventional technology (scientific analysis of traditional art works and its application to cutting-edge material technology).
The development process was as follows. Firstly, Dr. Shimode fabricated a top-grade lacquerware model for optical properties by coating a transparent resin plate with Japanese lacquer and polishing its surface by hand, repeatedly and then the Kyoto Institute of Technology and NEC scientifically analyzed the light reflection characteristics etc. of this lacquerware model. Finally, based on the evaluation and analysis results, NEC developed the optimum compound technology of additional ingredients to be mixed in the cellulose resin.
As a result of optical evaluation, the lacquerware model was found to exhibit an extremely low brightness (level 1) and the highest level (level 100) of glossiness, and furthermore, important features distinctive to Japanese lacquer: "depth and warmth". These features have not been quantified even with current optical analysis technologies, but Dr. Shimode's excellent sensitivity made it possible to sufficiently evaluate them.
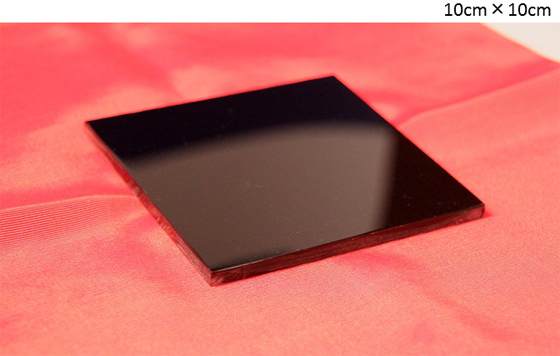

(Made by repeated manual coating of lacquer on a transparent plastic plate and polishing of the surface)
To attain the optical characteristics of the lacquerware model, various black colorants were added and mixed into cellulose resin. As a result, specific surface-treated carbon particles were found to lead to low brightness. To realize high glossiness, as well as using mirror-finished molds, addition of high-refractive-index organic compounds were investigated in order to enhance the glossiness of the material itself. High glossiness was realized by adding specific organic compounds with aromatic ring. Although there is usually a trade-off relationship between low brightness and high glossiness, optimization of the surface structures of the carbon particles and molecular structures of the high-refractive-index organic compounds lead to resolution of the trade-off. Further repeated adjustment of the compositions resulted in realization of "depth and warmth" of Japanese lacquer. It is possible that these features"depth and warmth" are influenced by the optical properties of the cellulose resin itself.
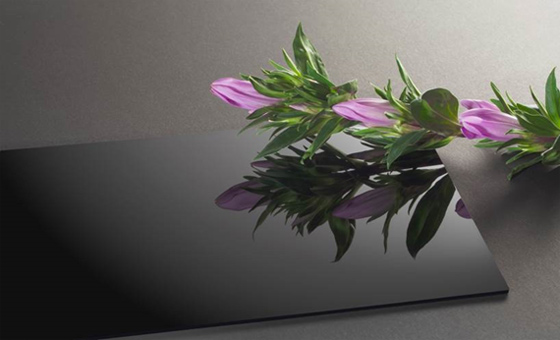



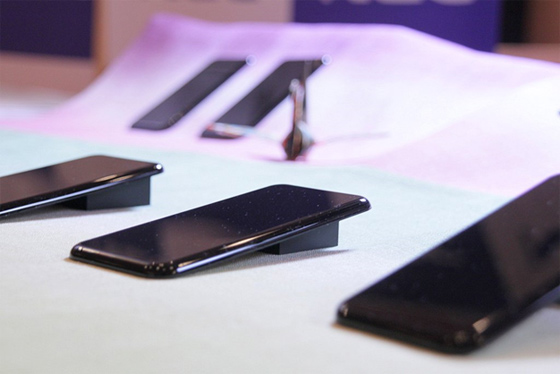

As for other characteristics of the bioplastic for practical usage, mechanical strength (bending, impact), surface hardness (pencil hardness), and thermoplasticity were brought to good levels (shown in the additional data of PDF). By further investigating the composition of the material, we will achieve higher levels of these characteristics: for an example, the levels for use in casing material of thin-type electronic products. Going forward, practical characteristics for each application and mass production technology will be accomplished.
Detailed data and characteristics of bioplastic are shown in an accompanying material (PDF).
Customers from diverse product fields have shown great interest in the new bioplastic: automobile interiors, building materials, and commodities, to name a few. We finally succeeded in a high-level makie-style printing and advanced scratch-proofing to keep the elegant appearance, which were anticipated by many of our customers (collaborative research with Dr. Shimode).
First, we achieved both the exquisite optical properties of high-grade lacquerware (low brightness, high glossiness, and the depth and warmth specific to Japanese lacquerware) and scratch-resistance by compound technology of unique additives that prevents wear from rubbing against cloth and paper. The "Urushi Black" tone bioplastic features lacquer-equivalent optical properties and the highest level of scratch-resistance among all decorative plastics, specifically, being able to maintain its glossiness after being rubbed with cloth 100 times.
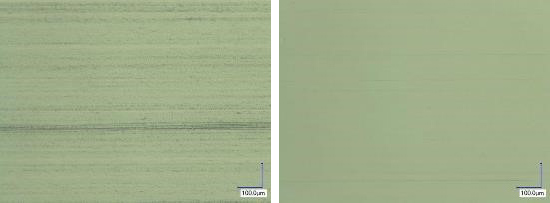
Left: Conventional "Urushi Black" bioplastic, Right: "Urushi Black" with improved scratch-resistance
Further, we used digital image processing to model the elaborate, three-dimensional, first-class makie drawn by Dr. Shimode. With the cooperation of a printing manufacturer with expertise in special printing, we optimized the ink composition, coloring components, and printing conditions. Through these processes, NEC succeeded in creating state-of-art makie-style printing that enables near faithful reproduction of the actual works.

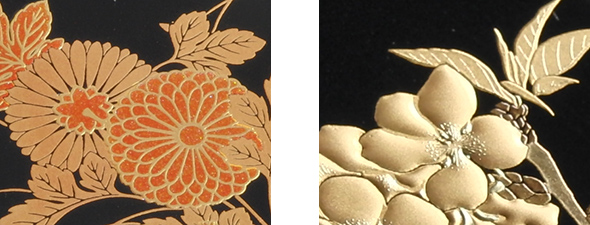
NEC will accelerate the practical application of non-edible, plant-derived bioplastics through the actualization of the new values: decorativeness and scratch-resistance.
NEC will pursue business partnerships with product producers to aim the expansion of the bioplastic to various products which requires decorativeness and environmental friendliness. Targeted applications of this "Urushi black" tone bioplastic are high grade general products such as watches, high-grade stationery, and cases for cosmetics and durable products such as interior parts of luxury cars, high-class building interior material or electronic products.
- (*1)Cellulose-type bioplastic (cellulose resin): Resin made using cellulose that is the main ingredient of the stems of cereal crops and wood, and is not suitable for human consumption. The resin is made by bonding short-chain fatty acids, such as acetic and propionic acid, or long-chain fatty acids to cellulose, which can be melted by heating (about 200 oC). This time, short-chain bonded cellulose resin, which is bonded with acetic and propionic acid, is used for the Urushi black bioplastic.
- (*2)Japanese lacquerware: Conventionally, Japanese lacquerware is made by substrate processing of the surface of wood products, manual coating with lacquer (a mixture of natural lacquer substance and coloring agents), and letting the lacquer harden, followed by repeated polishing of the product. It is highly regarded internationally as shown by the fact that lacquerware with makie (painting of figures on the surfaces) used to be known as "japan" because it progressed especially in Japan. Since manufacturing involves a tedious process, mass production as an industrial product is not possible.
- (*3)Japanese lacquerware artist, Dr. Yutaro Shimode: a third-generation president of Shimode makie-studio who is a leading lacquerware artist in Japan. He is a professor at the Faculty of Cultural Studies of Kyoto Sangyo University. His recent international engagements include being invited by the Ministry of Foreign Affairs of Japan to hold lectures and exhibits at famous museums in Europe.
(Ministry of Foreign Affairs website:https://www.mofa.go.jp/mofaj/files/000158375.pdf)
- (*4)Injection molding: Ordinary molding process for plastics. In this process, plastics are heated, melted, and injected into metal molds. By changing the shapes of the metal molds, products of various shapes can be mass-produced. Mirror-finished metal molds are used for the Urushi black bioplastic.
4. Commercialization and further development
As introduced above, we have been developed our original bioplastics: NeCycle TM, which achieve high plant ingredient ratios and high function used for electronic devises and used them in our products.
We then used this material (a high heat resistant kenaf fiber- reinforced polylactic acid composite) in commercial products such as NEC personal computers (La Vie TW and Versa Pro), dummy cards, and cell phones (FOMA-N701iECO). We further developed a safe, original flame retardant technology, and we succeeded in developing for practical use a flame-retardant polylactic acid composite is one of the most environmentally friendly flame retardant bioplastic in the world and is composed of more than 75 percent plant-based material. Then in January 2010, we used it in our line of eco-friendly business personal computers. Furthermore, to expand its use in various electronic equipment and other durable products, we have improved the resistances to chemical agents, scratch and light and anti-bacteria, which are higher than those of conventional petroleum-based plastics.
We have also developed bioplastic that has new recyclable and shape memory functions, and this technology holds great potential. With it we may be able to create new products such as wearable devices. We have continued to challenge the development of bioplastics with other new functions besides these and have succeeded in developing a bioplastic with thermal radiation and diffusivity comparable (greater than stainless steel) to metals. This new material will contribute to making thin and small mainstream electronic devices that are better able to diffuse heat and thus unharmful to the environment.
Currently we have been using crops that have become old and are used for livestock feed, but we are developing a new technology that will make it possible in the future to use only those parts of the plant that cannot be used, eaten, etc. (achieving a zero loss).
We have developed a new bioplastic using non-food plant based resources: cardanol-bonded cellulose resin. Furthermore, we have achieved in development of a new production process with a low energy consumption for the resin.
Aiming at applying the bioplastic using non-food biomass to various advanced products, we have tried to realize a new additional value, "decorativeness" (excellence in design) and then, have developed "Urushi black" tone bioplastic that embodies the exquisiteness of Japanese traditional lacquerware.(press-release August 17th, 2016, (press release February 6th, 2018) The offer of “Urushi black” tone bioplastisc samples has been started.)
We plan in the future to switch proactively from the petroleum based plastics we use now to these new bioplastics.
At NEC we will continue to expand our line-up and development of eco-products that use this type of original, environmentally friendly material. We will also expand and develop other environmentally responsible technologies such as those that reduce power consumption in electronic goods.